We are expanding
our material know-how
and test services with
the DEKRA laboratories!
Find out more in our
press release.
News:
Titanium alloys and titanium purity of medical instruments and implants according to
Accredited test laboratory
for materials testing, product testing & failure analysis.
Your specialist for metals,
plastics, elastomers.
We are expanding
our material know-how
and test services with
the DEKRA laboratories!
Find out more in our
press release.
News:
Titanium alloys and titanium purity of medical instruments and implants
according to DIN EN ISO 832
Accredited test laboratory
to DIN EN ISO / IEC 17025.
Your specialist for metals,
plastics, elastomers.
Failure analysis according to VDI guideline 3822.
Are you looking for a testing laboratory for a failure analysis or fracture analysis? When it comes to clarifying material failures or component faults, we offer expert support based on VDI 3822.
Our specialized team carries out in-depth damage analyses on plastics, metals and elastomer components as well as on composite materials and ceramics. These analyses are used in numerous industries, including medical technology, mechanical engineering and automotive engineering.
Example of a damage analysis metal / fracture types metal
Image documentation of a damage analysis on a broken rod end elevator.
A scanning electron microscope (SEM) is used to characterize defects, fracture surfaces, particles and reaction products under high magnification. An elemental composition is determined using integrated micro-range analysis (EDX).
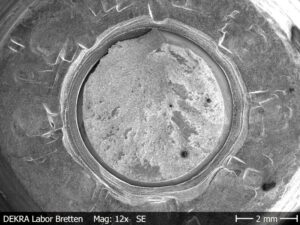
The fracture exit corresponds to a brittle grain boundary fracture - a classic case of material failure.

Thread imaged under an electron microscope
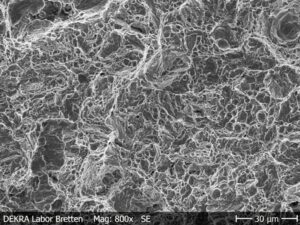
Ductile forced fracture (residual failure) - a typical form of fracture analysis
Example of a damage analysis for plastics
Clarification of technical damage cases through systematic fracture analyses (fractography) on thermoplastics and thermosets.
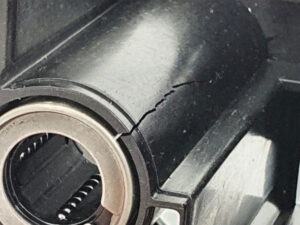
Fracture failure and crack formation on plastic components.
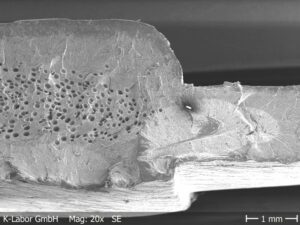
Analysis of damage-relevant, process-related material defects such as blowholes
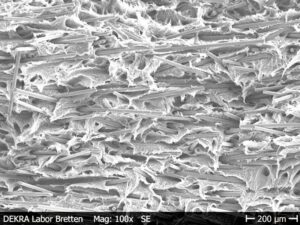
Evaluation of fiber-matrix adhesion in fiber-reinforced plastics - a common material failure in composites.
1. Damage analysis for plastic components
Plastics have become an integral part of modern applications – whether in the automotive, medical technology, electronics or packaging industries. Despite high performance, material failure can occur due to mechanical, chemical or thermal influences.
Our damage analyses in accordance with VDI guideline 3822 help you to systematically identify the causes of material and component failure and to develop preventive measures to avoid damage.
Typical cases of damage and fracture analysis of plastics:
- Fracture and crack formation: root cause analysis of embrittlement, crack growth and fatigue fracture
- Material fatigue: damage due to cyclic loading or environmental influences
- Processing defects: irregularities due to uneven cooling, blowholes or delamination
- Chemical degradation: resistance to solvents, acids, bases and other chemicals
- Thermal damage: analysis of material changes due to heat, UV radiation or oxidative degradation
- Adhesion problems in composites: Characterization of fiber-matrix adhesion in fiber-reinforced plastics
Systemic analysis methods for plastic components:
We use a variety of state-of-the-art testing methods to specifically determine the cause of damage:
- Scanning electron microscopy (SEM) incl. EDX analysis to examine fracture surfaces, defects and impurities
- Differential scanning calorimetry (DSC) to determine thermal properties and identify material changes
- Fourier transform infrared spectroscopy (FT-IR) to identify polymer compositions and foreign substances
- Thermogravimetric analysis (TGA) to examine thermal stability and decomposition temperatures
- Hardness tests (Shore A, D, IRHD, Vickers) for the mechanical characterization of plastics
- Tensile, bending and impact tests to determine mechanical strength and residual strength
Your added value through our damage analyses:
By combining systemic analysis and state-of-the-art measurement technology, we deliver reliable results for your quality assurance.
Our detailed investigations help you to identify sources of error in production, assembly or operation at an early stage. Preventive measures can avoid expensive production downtimes or complaints, which contributes to improved quality assurance and economic optimization in the long term.
2. Damage analysis for metallic components
Metallic materials are essential for numerous applications in industry, whether in mechanical and plant engineering, aerospace or automotive engineering. Despite their high strength and durability, metallic components are not immune to material failure. This can be caused by mechanical overload, material fatigue, corrosion or manufacturing defects.
With our fracture analysis in accordance with VDI guideline 3822, we precisely determine the cause of the damage and develop strategies based on this to prevent future failures.
Typical cases of damage to metallic components:
- Fracture failure: forced fracture, fatigue fracture, fatigue cracks, brittle fracture, sliding fracture
- Corrosion damage: crevice corrosion, pitting corrosion, fretting corrosion, intercrystalline corrosion
- Wear-related damage: abrasion wear, tribological wear, erosion wear
- Thermal damage: changes due to heat treatment, overheating or oxidation
- Weld seam defects: irregularities in welded joints, such as hot cracks, pores or bonding defects
Methods for failure analysis of metallic components:
We use state-of-the-art analysis methods to identify the causes of damage:
- Scanning electron microscopy (SEM) incl. EDX analysis to examine fracture surfaces, corrosion products and defects
- Vickers, Rockwell and Brinell hardness tests to assess mechanical properties
- Optical emission spectroscopy (OES) to determine the chemical composition of metals
- Metallographic examinations to analyze the microstructure and identify grain structures and microcracks
- Mechanical tests (tensile, bending and compression tests) to assess the strength of metallic materials
- Ultrasonic and X-ray testing for non-destructive analysis of internal defects and cracks
Your added value through our damage analyses:
Through a detailed analysis of metal damage, we help you to specifically identify the causes and develop suitable measures to prevent damage. This not only helps to increase component service life, but also reduces expensive downtime, rework and complaints.
With our modern testing methods and in-depth expertise, we support you in fault analysis, quality assurance and the development of robust, durable components.